Biofuels Support APRIL’s Renewable Energy Drive
APRIL’s commitment to sustainability extends beyond its plantation management, forest conservation and ecosystem restoration goals. It also includes the way it operates its mill.
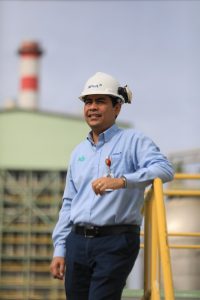
Eduward Ginting, Mill Operations Director
Eduward Ginting, Mill Operations Director, says the company’s long-term objectives are to continually increase the mill’s energy and water-use efficiency and also the use of renewable fuel sources. Of equal importance is the work towards establishing an accurate baseline for greenhouse gas emissions upon which to base reduction targets.
The key to achieving these goals, he says, is to keep finding innovative ways to capture and then recycle energy produced as part of the production process.
Located in Riau, Sumatra, the APRIL mill ranks as one of the most efficient in the world in terms of water and energy consumption, while producing up to 2.8 million tonnes of pulp and 1.2 million tonnes of paper annually.
This is achieved through operational and management incentives as well as a commitment to continuous improvement, or Kaizen method. This encourages lean manufacturing and the pursuit of efficiency and productivity.
APRIL re-uses most of its solid waste, such as wood chip residues, and black liquor, which are by-products of the process that converts wood chips into pulp.
“A total of 80% of the fuel we use is renewable, made up of by-product biomass and black liquor, recovered through four processing boilers. And for the past two years, we have reduced electricity consumption by optimising processes and finding innovative ways to improve efficiency,” says Ginting.
APRIL generates more than four million tonnes of biofuel per year, as well as about 16,000 tonnes of methanol, from black liquor through a process of evaporation and distillation. Introduced in 2010, this process produces a valuable methanol supply that is then used in the mill’s boiler as a substitute for fossil fuels.
“The methanol is derived from the stripping of gases from black liquor which then distilled to liquid methanol and use as a separate source of fuel for the mill in the boiler,” adds Ginting.
The mill’s water treatment facility processes about 265,000 cubic metres of water per day and about 89% of treated water is returned to the nearby Kampar River. “Reducing water consumption has been a big focus for us. Water consumption per unit product has actually been reduced by about 20% over the last four years,” he says.
The mill has the capacity to generate 525 megawatts, while currently needing about 390 megawatts. Some of the excess capacity is used to supply electricity to power the town of Kerinci, and supports the electricity needs of approximately 20,000 households in the area.
“We have managed to optimise production processes to consume much less energy, and reduced utility costs. We are promoting an environmentally-conscious approach in all we do,” says Ginting.
In addition to this, all emissions are regularly monitored and measured against global ISO standards for quality, and against other international standards for maintaining environmental, occupational safety and health standards.
A chemical engineer by training, he says several clean approaches have been implemented over the years, enabling far more sustainable practices and sources of energy. But Ginting says the bar is continuously being raised and there is no room for complacency.